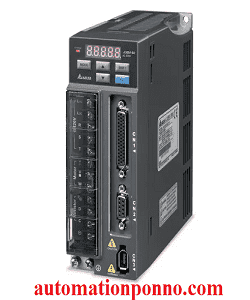
Delta ASD B2 1021 B
Ask Price WhatsApp: +8801713-722455
Description
The Delta ASD B2 1021 B is part of Delta’s ASDA-B2 series of servo drives, designed for high-performance motion control applications. It is suitable for small to mid-scale automation tasks, providing precision, speed, and stability. ASD B2 1021 B is the 1 kw servo drive of Delta electronics, if you need this servo drive you can contact BAT Power Solution Via email/WhatsApp: +8801713722455, see details asd b2 1021 b user manual
Material Features Delta ASD B2 1021 B
+Connects directly to 220V single phase
+(not to 3 x 380V!). Connects directly to 3 x 230V
+Rated output power: 1000 watts
+Step/Dir or analog input
+Position/speed/torque mode
+Auto-tuning of PID gain
Key Features
- Power Rating:
- This specific model has a power output of 1000W, making it suitable for smaller automation tasks that require precision.
- Control Modes:
- Supports Position Control, Speed Control, and Torque Control modes, allowing flexibility in how the drive interacts with the servo motor.
- High Precision:
- Paired with a 17-bit or 20-bit incremental encoder, this drive offers high-precision positioning, ideal for applications requiring fine control over movement and positioning.
- Communication:
- The drive supports RS-485 communication using the Modbus protocol, making it easy to integrate with other control systems such as PLCs or HMIs.
- Compact Design:
- The ASDA-B2 series is known for its compact size, making it easy to install in limited spaces while maintaining high functionality.
- Easy Tuning and Setup:
- The drive features auto-tuning functions, simplifying the setup process and ensuring optimal performance with minimal manual configuration.
Implements high precision positioning control
► ASDA-B2 series servo drives support 17-bit Encoder & 20-bit encoders. It satisfies the demand of high-precision position control and stable operation with low speed.
► Applying encoders with higher resolution can reduce cogging torque and improve motor accuracy.
Satisfies the needs of a wide variety of industries
► Three control modes are available: built-in position, speed and torque.
► High speed differential command (up to 4Mpps) for high precision position control.
► Three notch filters are provided to efficiently suppress mechanical resonance and make the system operate more smoothly.
► Lead friction compensation parameters are specified for circular interpolation, Z-axis motion and ball screw, and other applications to reduce controller loading.
► For bar feeders and other equipment requiring high torque output,
Motor protection parameters are provided to protect the mechanical system.
► The ASDA-B series shares the same power cable and encoder cables for easy installation and setup without additional accessories.
► Servo motors offer brakes, oil seals and other optional configurations for various applications.
► Separate power supply mechanism for main circuit and control circuit makes it easy to maintain.
► 400W or above servo drives have built-in regenerative resistors, which simplify wiring and reduce installation costs.
► Separate connectors (2 sets) for analog signal output, also simplifying wiring.
Applications:
- Robotics: Used in robotic arms for precision movements.
- CNC Machinery: Ideal for controlling the movement of parts in machines that require accurate positioning.
- Packaging: Ensures that packaging machinery operates smoothly and efficiently.
- Conveyors: Provides speed control and accuracy for material handling systems.
Specification of ASD-B2-1021-B
Model Name | ASD-B2-1021-B |
Series | B2 Servo Drive |
Phase | 1/3 PH |
Voltage | 220 VAC |
Rated Output Power | 1000 W |
ASDA-B2 Series | 100 W | 200 W | 400 W | 750 W | 1 kW | 1.5 kW | 2 kW | 3 kW | ||
1 | 2 | 4 | 7 | 10 | 15 | 20 | 30 | |||
Power Supply | Three-phase 170 ~ 255 VAC , 50/60 Hz ±5% | Three – phase | ||||||||
Phase / Voltage | 170 ~ 255 VAC, 50 / 60 Hz | |||||||||
Single-phase 200 ~ 255 VAC , 50/60 Hz ±5% | ±5% | |||||||||
Input Current (3PH) (Units: Arms) | 0.39 | 1.11 | 1.86 | 3.66 | 4.68 | 5.9 | 8.76 | 9.83 | ||
Input Current (1PH) (Units: Arms) | 0.69 | 1.92 | 4.5 | 6.78 | 8.88 | 10.3 | – | – | ||
Continuous Output Current (Units: Arms) | 0.9 | 1.55 | 2.6 | 5.1 | 7.3 | 8.3 | 13.4 | 19.4 | ||
Cooling System | Natural Air Circulation | Fan Cooling | ||||||||
Encoder Resolution | 17-bit (160,000 p/rev) | |||||||||
Main Circuit Control | SVPWM (Space Vector Pulse Width Modulation) Control | |||||||||
Control Mode | Auto / Manual | |||||||||
Regenerative Resistor | None | Built-in | ||||||||
Position Control Mode | Max. Input Pulse Frequency | Transmitted by differential: 500 K (low speed) / 4 Mpps (high-speed) Transmitted by open-collector: 200 Kpps | ||||||||
Pulse Type | Pulse + Direction, A phase + B phase, CCW pulse + CW pulse | |||||||||
Command Source | External pulse | |||||||||
Smoothing Strategy | Low-pass filter | |||||||||
E-gear Ratio | Electronic gear N/M multiple N: 1 ~ (226 -1) / M: 1 ~ (231 -1) (1/50 < N/M < 25600) | |||||||||
Torque Limit Operation | Set by parameters | |||||||||
Feed Forward Compensation | Set by parameters | |||||||||
Speed Control Mode | Voltage Range | 0 ~ ±10 VDC | ||||||||
Analog Input | Input Resistance | 10 KΩ | ||||||||
Command | Time Constant | 2.2 μs | ||||||||
Speed Control Range*1 | 3.513888889 | |||||||||
Command Source | External analog signal / Internal parameters | |||||||||
Smoothing Strategy | Low-pass and S-curve filter | |||||||||
Torque Limit | Set by parameters or via analog input | |||||||||
Bandwidth | Maximum 550 Hz | |||||||||
±0.01% at 0 to 100% load fluctuation | ||||||||||
Speed Accuracy *2 | ±0.01% at ±10% power fluctuation | |||||||||
±0.01% at 0 oC to 50 oC ambient temperature fluctuation | ||||||||||
Torque Control Mode | Voltage Range | 0 ~ ±10 VDC | ||||||||
Analog Input | Input Resistance | 10 KΩ | ||||||||
Command | Time Constant | 2.2 μs | ||||||||
Command Source | External analog signal / Internal parameters | |||||||||
Smoothing Strategy | Low-pass filter | |||||||||
Speed Limit | Set by parameters or via analog input | |||||||||
Analog Monitor Output | Monitor signal can set by parameters (Output voltage range: ±8 V) | |||||||||
Servo on, Fault reset, Gain switch, Pulse clear, Zero clamp, Command input reverse control, Torque limit, Speed limit, Speed command selection, Speed / position mode switching, Speed / torque mode switching, Torque / position mode switching, Emergency stop, Positive/negative limit, Forward / reverse operation torque limit, Forward/reverse JOG input, E-gear N selection, Pulse input prohibition | ||||||||||
Input | ||||||||||
Digital Input / | Encoder signal output (A, B, Z Line Driver / Z Open collector) | |||||||||
Output | Output | Servo on, Servo ready, Zero speed, Target speed reached, Target position reached, Torque limiting, Servo alarm, Brake control, Early warning for overload, Servo warning | ||||||||
Over current, Overvoltage, Under voltage, Overheat, Excessive speed deviation, Excessive position deviation, Encoder error, Emergency stop, Communication error, Short-circuit protection of terminal U, V, W and CN1, CN2, CN3 | ||||||||||
Protective Functions | ||||||||||
Communication Interface | RS-232 / RS-485 | |||||||||
Environment | Installation Site | Indoor location (avoid direct sunlight), no corrosive liquid and gas (avoid oil mist, flammable gas, dust) | ||||||||
Altitude | Altitude 2000 m or lower above sea level | |||||||||
Atmospheric Pressure | 86 kPa ~ 106 kPa | |||||||||
Operating Temperature | 0 ºC ~ 55 ºC (If operating temperature is above 45 ºC, forced cooling will be required) | |||||||||
Storage Temperature | -20 ºC ~ 65 ºC (-4 ºF to 149 ºF) | |||||||||
Humidity | 0 to 90% (non-condensing) | |||||||||
Vibration | Under 20 Hz, 9.80665 m/s2 (1G), 20 ~ 50 Hz 5.88 m/s2 (0.6 G) | |||||||||
IP Rating | IP20 | |||||||||
Power System | TN System*3 | |||||||||
Certification | IEC/EN 61800-5-1 |
Compatibility:
- It is typically paired with Delta ECMA-series servo motors, such as the ECMA-C10604RS, to provide a complete motion control solution. others products
Reviews
There are no reviews yet.